- Published: 2024-01-13
- Updated: 2025-08-26
- Post rating: 4.5
- MeshLib Team
Precision Mesh
Offsetting with MeshLib
Mesh Offsetting is an important technique in 3D geometry processing. It creates a surface that’s parallel to the original mesh at a set distance. This allows for exact growth or shrinkage of solid objects. Many industries use this process. In 3D printing, it helps ensure proper wall thickness and support structures.
MeshLib offers advanced Mesh Offset features that improve 3D modeling and manufacturing. This useful tool lets users make parallel surfaces at specific distances from the original meshes. It’s crucial for industries like 3D printing, CNC machining, and injection molding. MeshInspector’s Offset tool gives users great control over surface thickness. This makes work more precise and efficient in many areas.
What Mesh Offsetting modes does MeshLib offer?
MeshInspector’s Offset tool has five different offset modes, each designed for specific modeling needs:
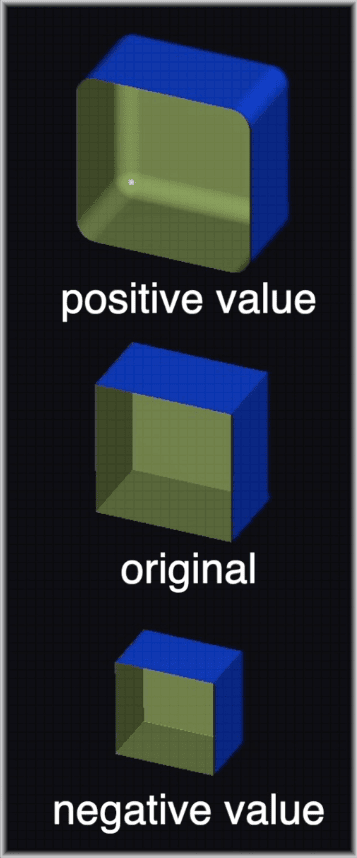
1. Entire Model Offset Mode
- Purpose: Offsets the whole mesh evenly
- Function: Positive values expand, negative values contract
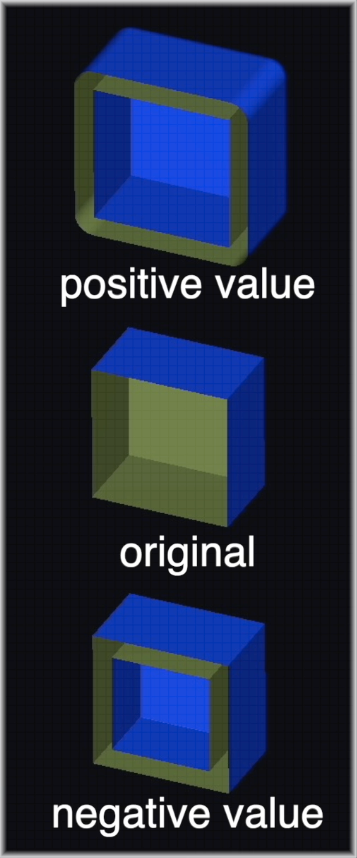
2. Thickening Mode
- Purpose: Adds an extra surface layer
- Function: Positive values add an outer layer, negative values add an inner layer
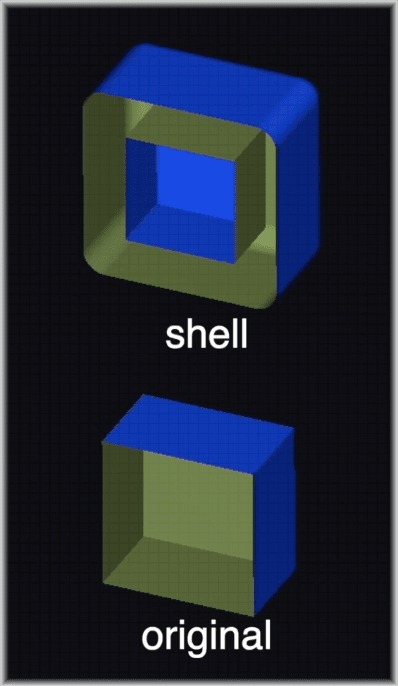
3. Shell Mode
- Purpose: Makes two new surfaces and removes the original mesh;
- Ideal for: Creating hollow parts in mold making.
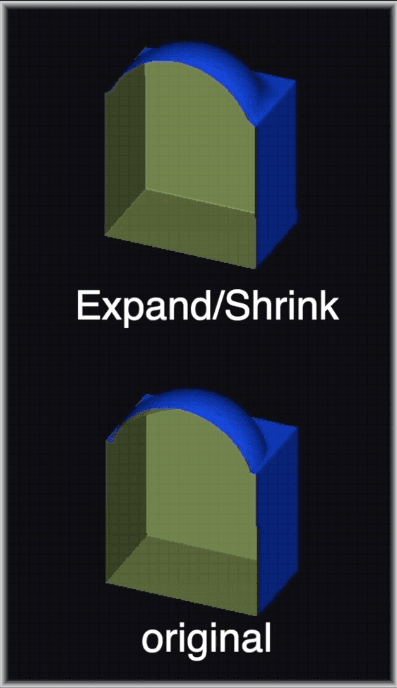
4. Expand/Shrink Mode
- Purpose: Smooths inward curves and increases volume;
- Process: First expands, then shrinks the mesh.
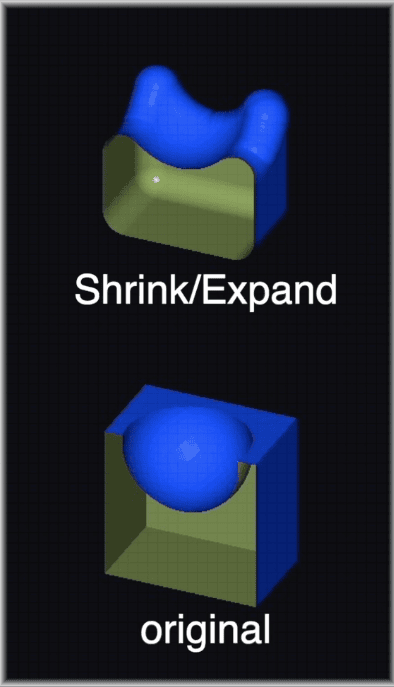
5. Shrink/Expand Mode
- Purpose: Smooths outward curves and decreases volume
- Process: First shrinks, then expands the mesh
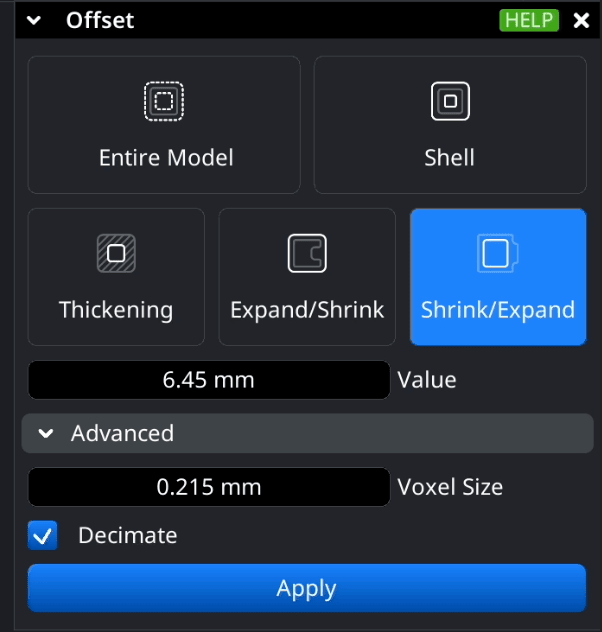
5.1 Advanced settings
Advanced settings let users fine-tune the offset process:
- Voxel Size controls surface detail level.
- Decimation simplifies the created surface to work better.
Here is the example of mesh offset code in MeshLib:
import meshlib.mrmeshpy as mrmeshpy
# Load mesh
mesh = mrmeshpy.loadMesh("mesh.stl")
# Setup parameters
params = mrmeshpy.OffsetParameters()
params.voxelSize = mesh.computeBoundingBox().diagonal() * 5e-3 # offset grid precision (algorithm is voxel based)
if mrmeshpy.findRightBoundary(mesh.topology).empty():
params.signDetectionMode = mrmeshpy.SignDetectionMode.HoleWindingRule # use if you have holes in mesh
# Make offset mesh
offset = mesh.computeBoundingBox().diagonal() * 0.05
result_mesh = mrmeshpy.offsetMesh(mesh, offset, params)
# Save result
mrmeshpy.saveMesh(result_mesh, "offsetMesh.stl")
#include
#include
#include
#include
#include
#include
int main()
{
// Load mesh
MR::Mesh mesh = *MR::MeshLoad::fromAnySupportedFormat( "mesh.stl" );
// Setup parameters
MR::GeneralOffsetParameters params;
params.voxelSize = mesh.computeBoundingBox().diagonal() * 5e-3f; // offset grid precision (algorithm is voxel based)
if ( !MR::findRightBoundary( mesh.topology ).empty() )
params.signDetectionMode = MR::SignDetectionMode::HoleWindingRule; // use if you have holes in mesh
// Make offset mesh
float offset = mesh.computeBoundingBox().diagonal() * 0.05f;
auto meshRes = MR::generalOffsetMesh( mesh, offset, params );
if ( !meshRes.has_value() )
{
// log meshRes.error()
return 1;
}
// Save result
MR::MeshSave::toAnySupportedFormat( *meshRes, "mesh_offset.stl" );
return 0;
}
Find more examples in our documentation
Industries benefiting from using MeshLib's Mesh Offset
MeshLib’s Mesh Offset features offer numerous advantages in many fields:
3D Printing
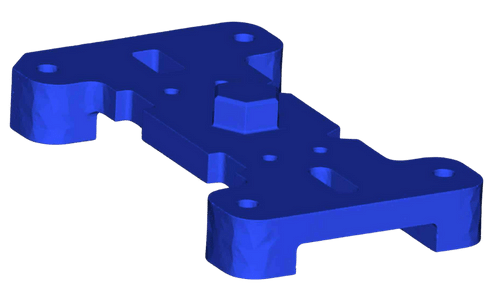
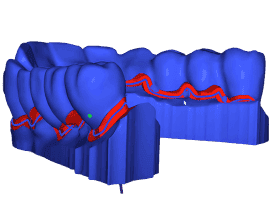
In 3D printing, Mesh Offset allows exact control of wall thickness, better support structures, and improved print quality.
Dental Industry
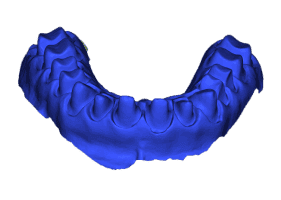
Dentists use Mesh Offset to design custom aligners and dental devices, ensuring they fit well and feel comfortable.
Why choose MeshLib SDK for Mesh Offsetting?
MeshLib leads in 3D processing, offering top-notch Mesh Offsetting that’s fast, precise, and versatile. It’s an open-source 3D geometry library that works with C++, C#, and Python, fitting easily into different projects and speeding up development. Its advanced methods and GPU boost make offsetting up to 10 times faster than other options, giving high-quality results even for complex meshes.
MeshLib works on different platforms and has a modern design without old limitations. This makes it the top choice for professionals who want to push the limits of 3D modeling and manufacturing in fields like 3D printing, CNC machining, and medical device design.
What our customers say
Thomas Tong
Founder, Polyga
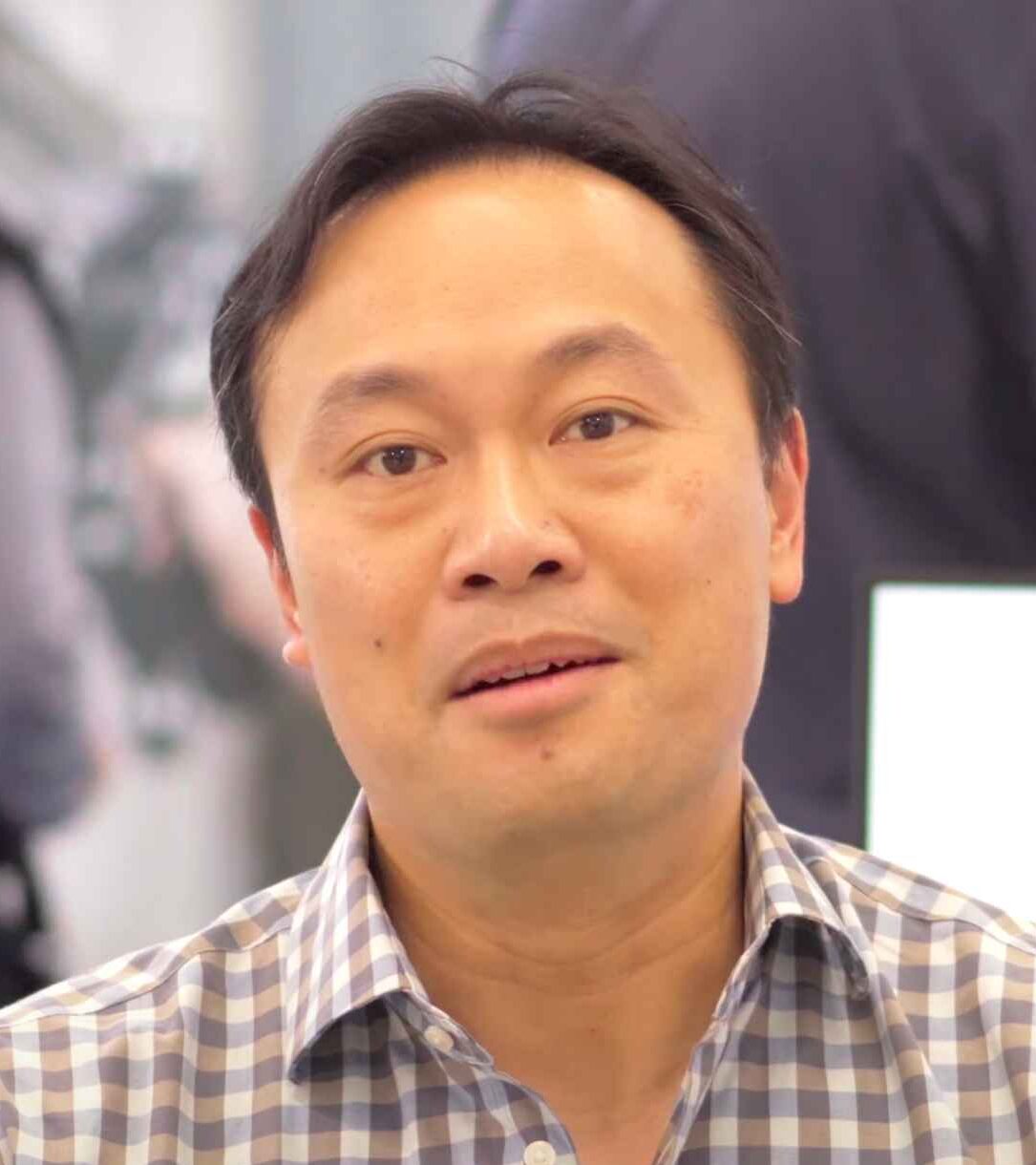
Gal Cohen
CTO, customed.ai
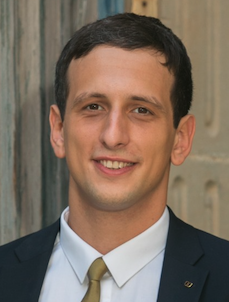
Mariusz Hermansdorfer
Head of Computational Design at Henning Larsen Architechts
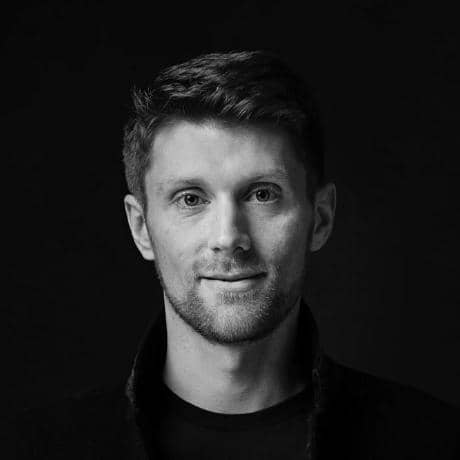
HeonJae Cho, DDS, MSD, PhD
Chief Executive Officer, 3DONS INC
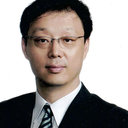
Ruedger Rubbert
Chief Technology Officer, Brius Technologies Inc
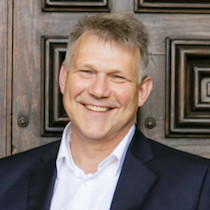
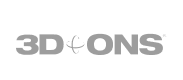
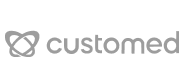
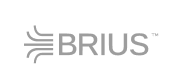
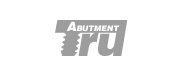
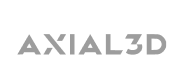
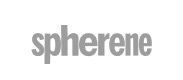
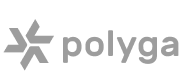
Conclusion
MeshLib’s Mesh Offset features help professionals in many industries achieve new levels of precision and efficiency in their 3D modeling and manufacturing work. Using MeshInspector’s Offset tool, users can confidently tackle complex geometric challenges and produce better results.
Unlock the full potential of Mesh Offsetting with the MeshInspector with in-depth tutorials and demonstrations on our YouTube channel! Watch how MeshLib’s powerful tools can transform your 3D modeling and manufacturing processes.
Start Your Journey with MeshLib
MeshLib SDK offers multiple ways to dive in — from live technical demos to full application trials and hands-on SDK access. No complicated setups or hidden steps. Just the tools you need to start building smarter, faster, and better.
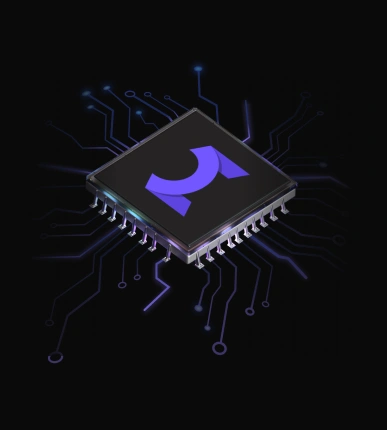
- Post rating: 4.5